Digital Transformation and Business Resilience in Action: A Look into UPS’s Visionary Approach to Automation, AI and Analytics
UPS's digital transformation was years in the making. This is how it paid off big time in 2020.
Add bookmark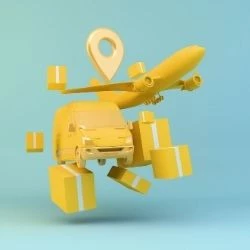
Since the onset of the pandemic this past spring, parcel delivery providers such as UPS have served as a lifeline for many Americans stuck at home during the pandemic. Practically overnight, shipping volumes skyrocketed to 60% leaving many parcel delivery providers scrambling to fulfill orders while also ensuring the safety and wellbeing of their workforces.
Given that the pandemic and the resulting surge in online shopping was wholly unexpected, UPS in particular has done a remarkable job of ensuring parcels arrive on time. Even at the height of the pandemic this spring, UPS was able to maintain a on-time delivery rate of 98% in April and 95.4% in May, representing only a .4-2.6% reduction YOY. Considering on-time delivery rates for the industry as a whole dropped to 75-79% during these months, these figures are really quite impressive.
By December 2020, UPS was not only maintaining previously held average transit times, they were beating them. Launched during the first week of November, UPS’s “Fastest Ground Ever” initiative successfully reduced delivery times by an average of one day for millions of Americans in just a matter of weeks.
The secret to UPS’s success? For decades, UPS has made solid investments in its IT infrastructure and data architecture, primarily, to maximize the speed at which packages are delivered. Though UPS could not have predicted the COVID-19 pandemic itself, having a solid “digital backbone” in place beforehand certainly put the company in a better position to confront the immense challenges brought on by this crisis.
UPS’s $20 Billion Bet
In 2018, UPS made headlines when they announced that they would be investing over $20 billion dollars into their e-commerce operations. Though investors were skeptical, those investments are clearly paying off.
One area UPS has invested heavily in over the past two years is transforming facility hubs into, essentially, data and analytics command centers. Using a sophisticated array of IoT sensors, cameras and a state-of-the-art big data solution known as Network Planning Tools (NPTs), UPS is able to track the roughly 2 million packages per day the facility processes per day as they travel through the system.
However, NPTs does more than track than track these packages. By combining internal tracking data with external data (weather and traffic), UPS’s Network Planning Tools (NPTs) provides “a bird’s-eye view of the volume in the network and the peaks and valleys that are expected,” according to TechRepublic. In other words, it leverages predictive and prescriptive insights to scale operations based on volume and optimize efficiency. Infact, the NPTs tool was the key enabling technology behind the “Fastest Ground Ever” initiative mentioned above that successfully reduced delivery times to 3 days or less for 90% of Americans.
ORION
Starting in 2008, UPS installed more than 100,000 Smart Trailer devices to track the movements of delivery trucks and other company assets. By mining the estimated 60 million GPS messages these systems produce every week, UPS is able to identify inefficiencies and optimize transit routes.
To do this, UPS created ORION, which stands for “on-road integrated optimization and navigation,” a system that uses fleet telematics and advanced algorithms to continuously optimize delivery routes in terms of distance, fuel, time and environmental impact. Used in conjunction with NPTs, ORION can analyze over 250 million data points in a matter of seconds and produce tens of thousands route enhancements per minute.
Since its original deployment in 2013, UPS has expanded ORION’s capabilities to incorporate additional relevant externalities such as weather, traffic or vehicle maintenance needs into its analysis. Not only does this predictive insight help ensure packages arrive on time, but that vehicles are proactively maintained and drivers can avoid hazardous driving conditions.
Since its deployment in 2013, ORION has already reduced driver routes by an estimated 100 million miles. Considering a reduction of just one mile per driver per day over one year can save UPS upwards of $50 million, the savings generated by ORION are significant to say the least.
In an interview with TechRepublic, UPS CIO Juan Perez said of ORION, “In the future, which is next year, we will be doing all those optimizations dynamically, which means that, as the driver is making deliveries throughout the day, he or she will be presented with enhancements, improvements to the route so that the driver can become more efficient, continue to make all of our service commitments to our customers, and continue to be more sustainable.
Last Mile Delivery Accelerated
In addition to investing in digitizing logistics operations behind the scenes, UPS has also used these systems to optimize customer-facing services and products. Ever tracked a UPS package online or via the mobile app? The tracking information you see is supplied by the ORION system.
UPS has also developed AI-powered chatbots to help customers with simple queries such as parcel tracking, shipping rates, retail locations, etc. The data from these applications is fed directly into the NPTs where it is synthesized, analyzed and, eventually, used to optimize the customer journey.
December 2020: The Ultimate Test for Business Resilience
As the pandemic rages on and people remain stuck at home, an estimated 3 billion packages will travel through the nation’s shipping infrastructure this holiday season, according to the New York Times. This record breaking number is about 800 million more than delivered last year.
On top of that, UPS has been tapped to serve as the primary distributor of the COVID-19 vaccine. In fact, the first shipment of COVID-19 vaccinations went out the week of December 13th also happened to be the busiest shopping/shipping week of the year.
In order to accommodate a historically busy holiday season while also, much more importantly, ensuring the safe and timely arrival of COVID-19 vaccinations, UPS spent millions on automation, technology and cooling solutions. For example, UPS has outfitted each kit with a specialized tracking device that supports real-time monitoring of temp and location.
In Summary
Throughout the COVID-19 crisis, UPS relied on advanced analytics and AI-based techniques to make fast, evidence-based decisions and build upon existing capabilities. The technology and data infrastructure UPS has set up over the past few years has enabled them to do more than just increase the speed of delivery (which was the original intention) but thrive during a time of great uncertainty, unrest and volatility. While many of their competitors struggled to keep up with the challenges posed by the pandemic, UPS very publicly outperformed many of its competitors. This has not gone unnoticed by Wall Street as stock prices for UPS continue to rise.
Though pandemics and other disasters are impossible to predict, they are inevitable. As for pandemics specifically, evidence suggests that they are becoming more frequent. The data UPS has gathered throughout the pandemic and is gathering as they help distribute the vaccine will not only help them ensure they are prepared as possible for the next large-scale disaster in terms of business continuity, but could also shed light on how government agencies and healthcare organizations can better distribute life saving supplies and treatments in the future.
When it comes to innovation, UPS shows no sign of slowing down. According to reports, UPS is already experimenting with data-driven, cutting-edge solutions such as drone delivery and geo-fenced autonomous vehicles.